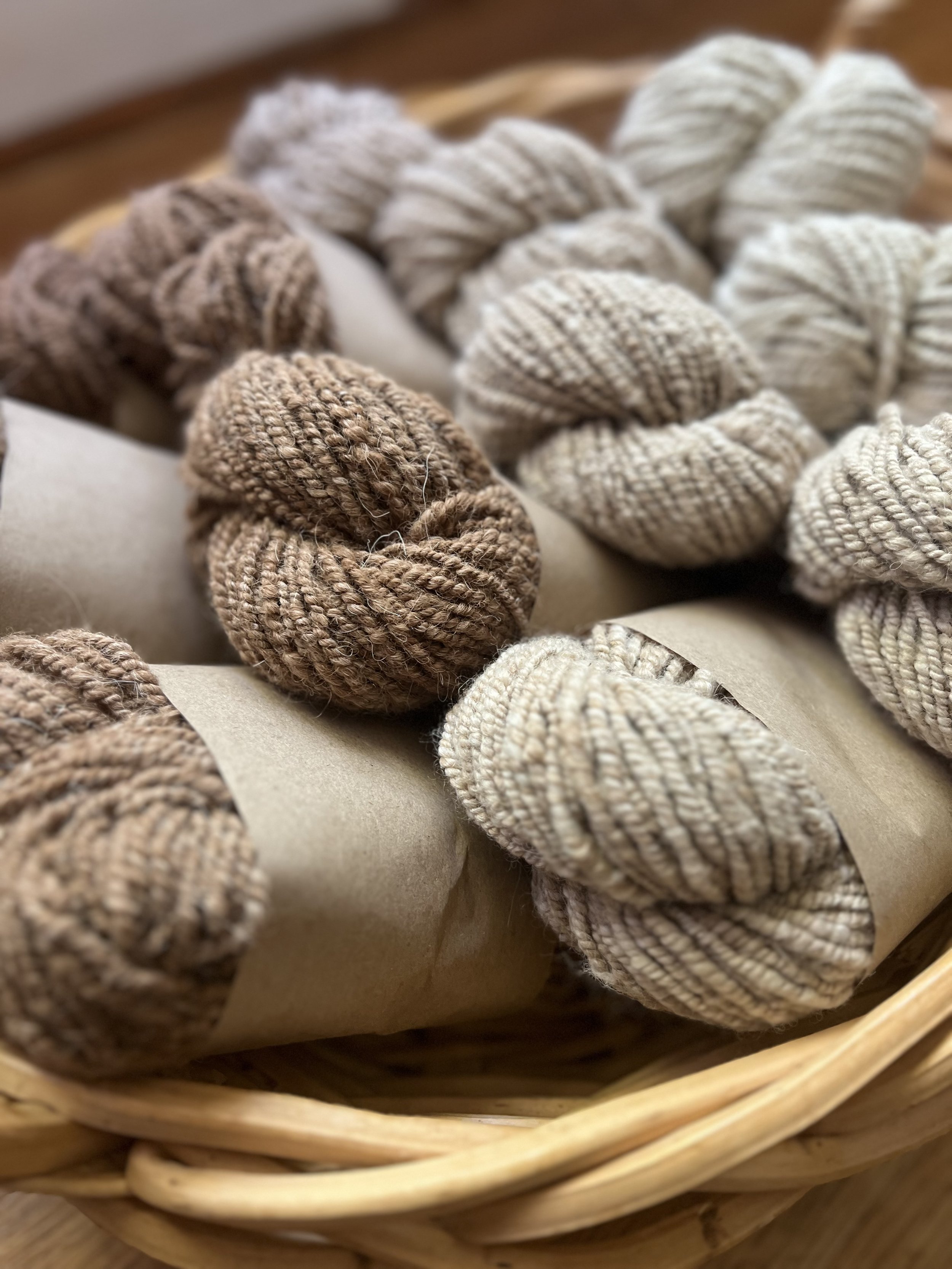
We’re here to help with all your fiber
& wool processing needs.
NOW PROCESSING WITH BELFAST MINI MILLS EQUIPMENT
Watch below for a roving demonstration!
Our Processing Services.
We specialize in cleaning, carding, roving, and spinning your fibers with care. Whether you’re a small-scale farmer, artisan, or fiber enthusiast, our services ensure that your raw fibers are treated with the respect and skill they deserve.
**Please note for returning customers that as of 2025, prices are no longer cumulative and have been updated below accordingly.
-
Sorting, Washing, Scouring, & Picking
Based on the incoming weight. We wash all fiber and reserve the right to remove debris as necessary to produce quality results prior to washing.
EXTRA GENTLE SYSTEM!
Note: this kind of wash is really a hot soak with Unicorn Power Scour, then spin, rinse, another wash, spin, then two rinses and a spin without agitation to remove dirt and lanolin/oils. This washing will not take out straw, burs, chip, or vegetable matter. We will either do that by hand, or with the picker using the Belfast Mini Mills Picker. Excessive vegetation will be charged at next higher rate. Unfortunately if that is the case, only 90-95% removal of guard hairs and vegetation is possible generally.
-
Carding to Batts or Rovings
Based on incoming weight. Picking and carding prepares the fiber to spin or felt by brushing out any additional debris and aligning individual fibers into a singular direction. We recommend rovings if you’re interested in having your fiber processed to spin yourself.
Batts (approx. 2 feet wide by 4 feet long -- thickness determined by weight)
Roving (approx. 1 inch dia.) loose in a bag or wound into a log-shaped "bump."
100% Alpaca or Llama roving can be complex, as we cannot tell from inspecting a bag of raw alpaca whether it will produce a cohesive enough web to be pulled through our roving deck. If it does not, simply falling off our swift and drifting apart after the doffer comb, we will continue to card the fleece to cloud and return it to you as cloud. We do not stock generic wool to blend at this time, nor a range of colors to match your alpaca. We simply cannot substitute our judgment of the quantity, quality, and kind of wool you would like to have blended with your alpaca to make it run on our carder and roving deck.
The safest bet for alpaca roving is to blend a minimum of 25% wool – sheep wool (long wools are often not effective). -
Spinning
All fiber is then processed into single ply, homespun yarn or 2-ply. Currently all spinning is done by hand, so if you want your fiber spun it may take additional processing time, which will be projected in your quote.
-
Dryer Balls
Based on incoming weight. A great way to utilize seconds or fiber not useable for other projects.
-
Felted Coasters
Based on incoming weight. A great way to utilize seconds or fiber not useable for other projects.
-
Knitted Products
We offer knitted hats and headbands with your yarn if you’re looking for finished products.

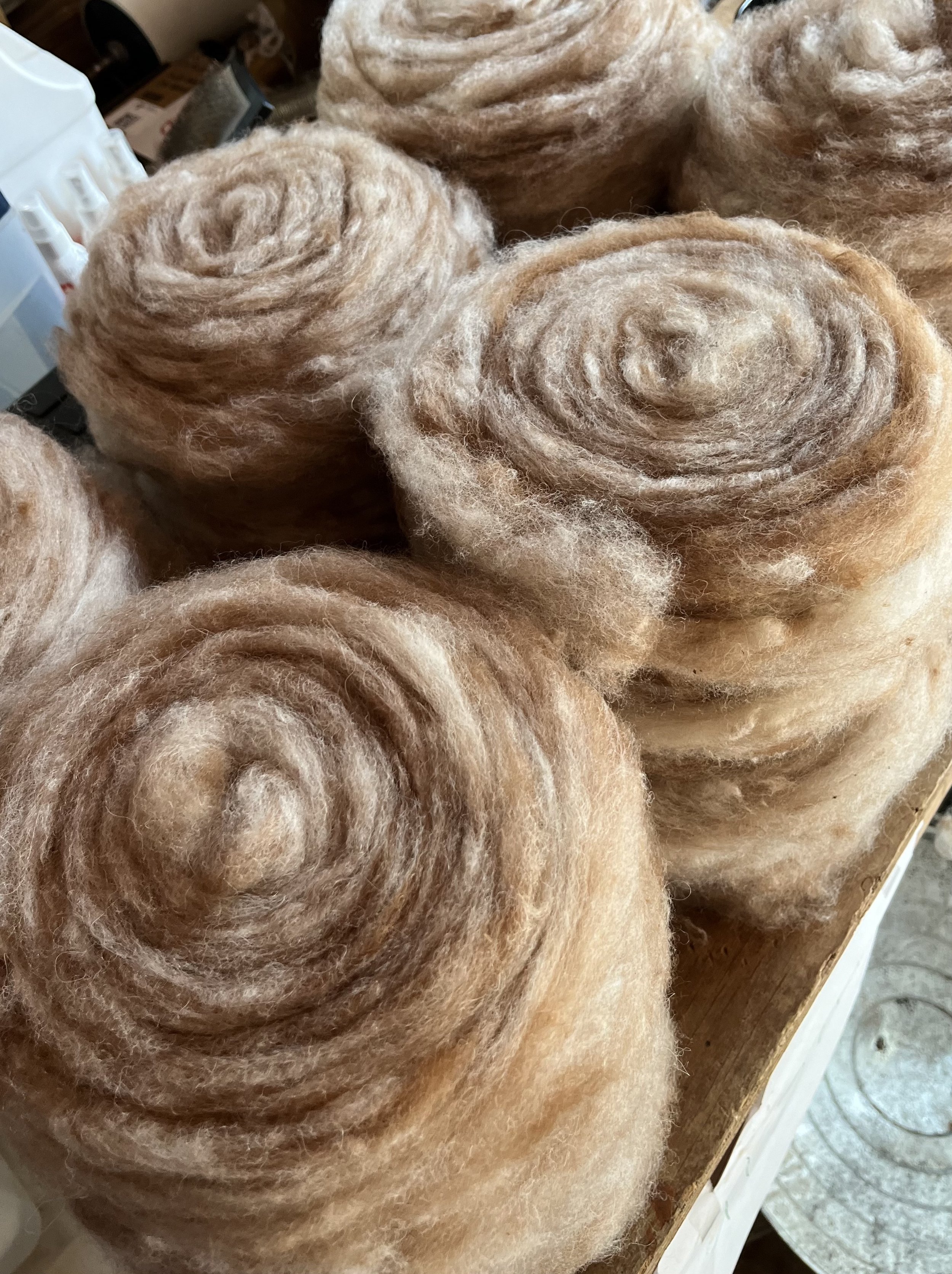
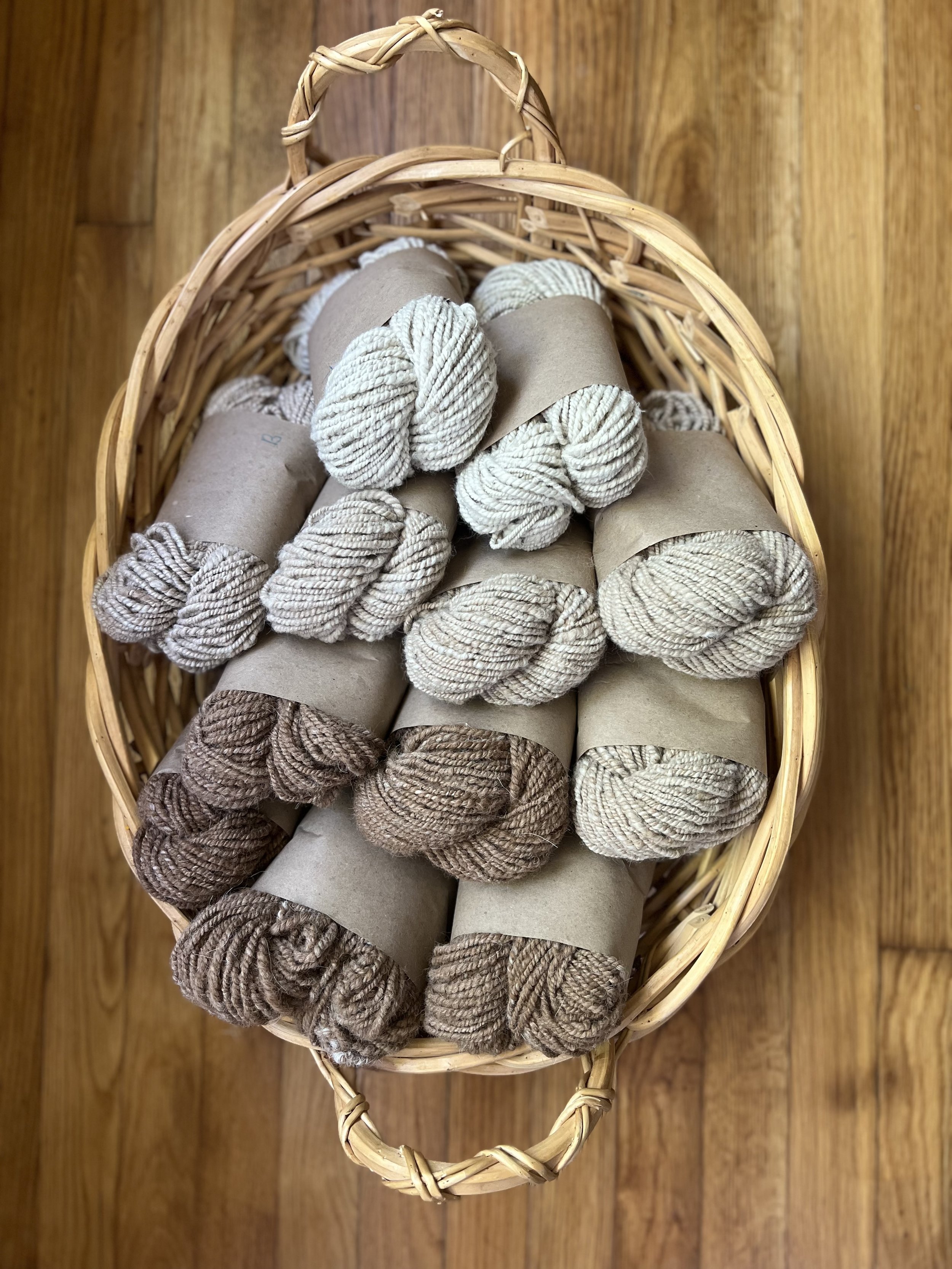
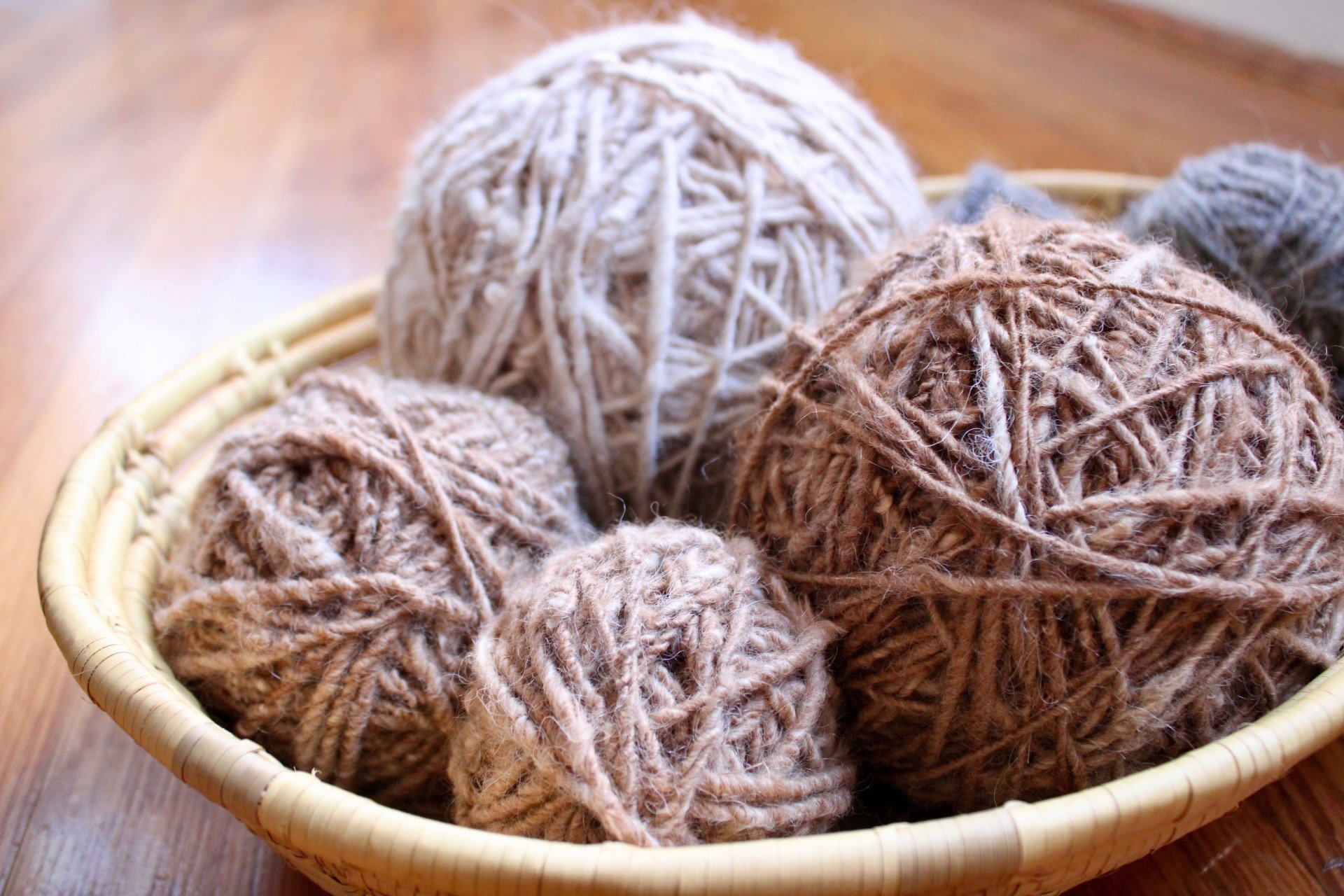
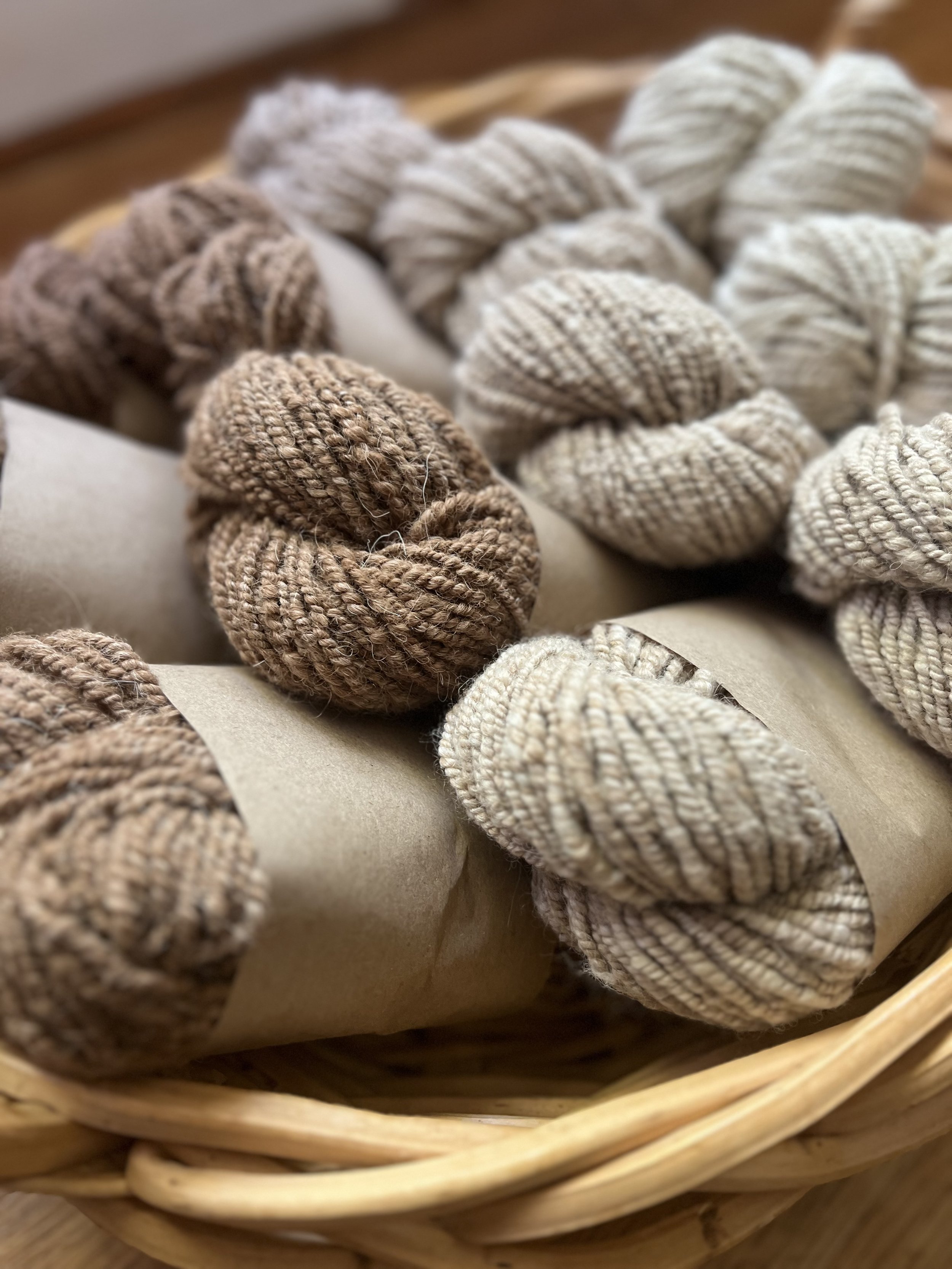
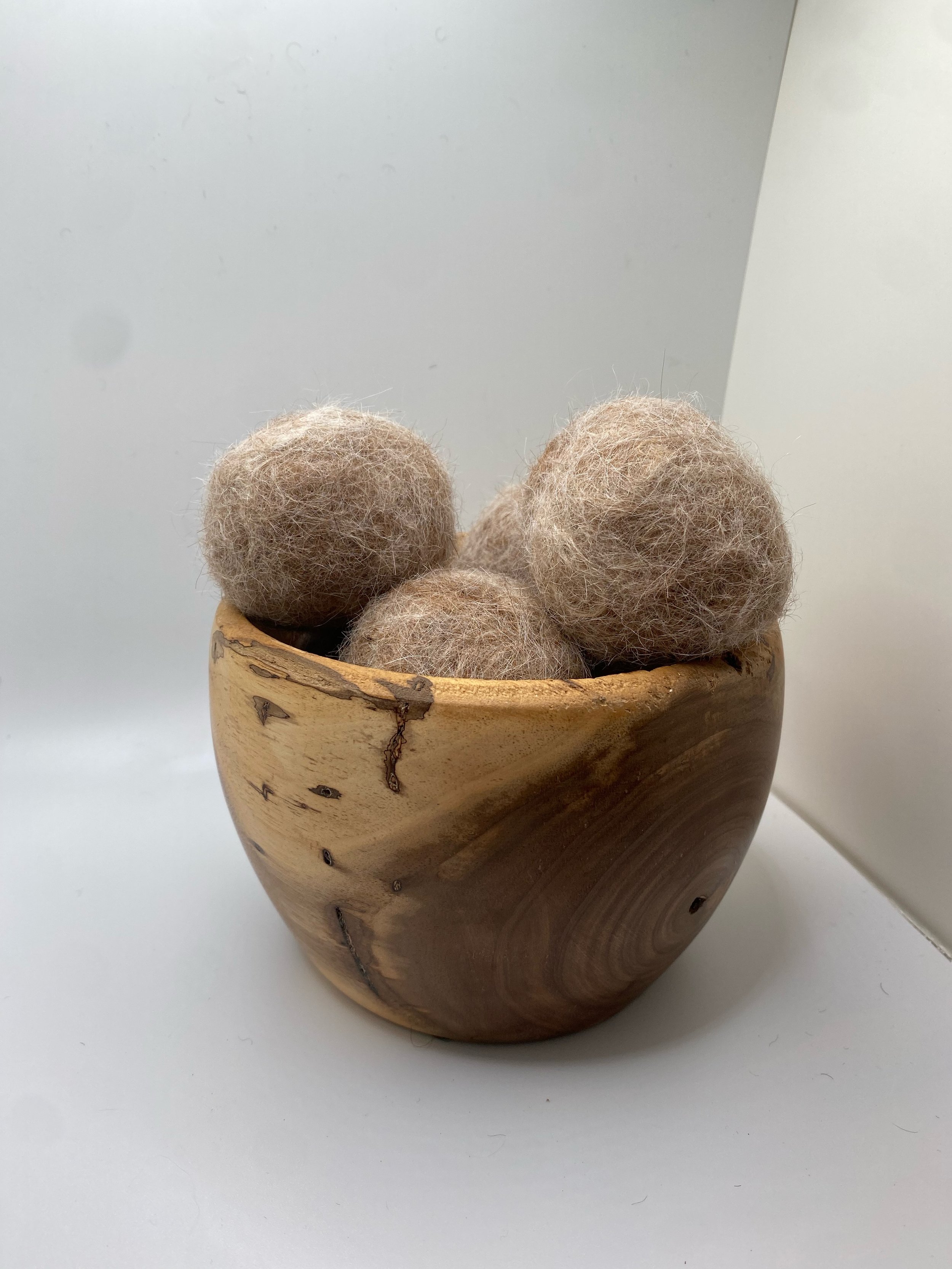
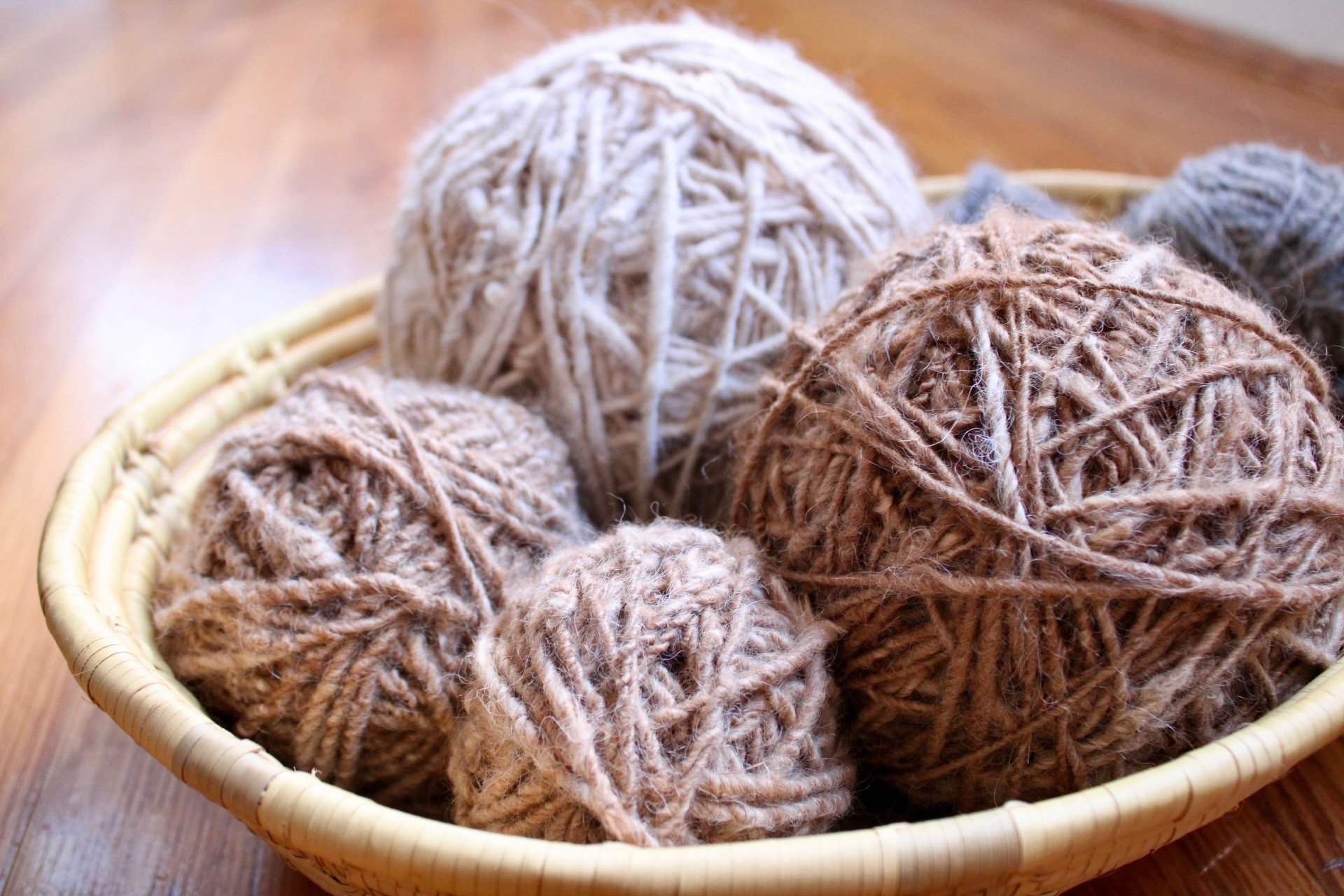
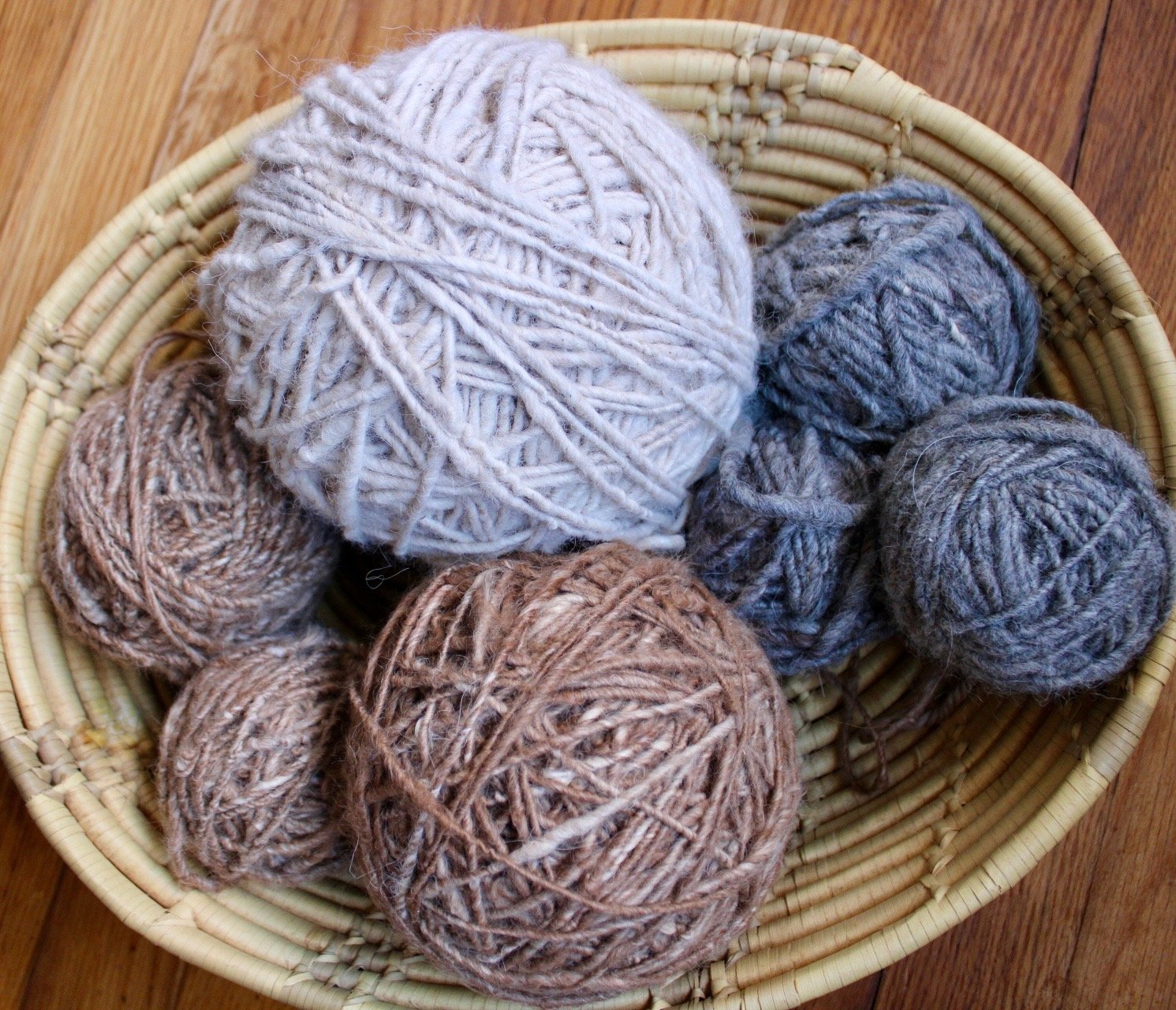
Receive a fiber processing quote.
FIBER FAQS & POLICIES
If your question or concern is not addressed below, please do not hesitate to reach out to us via goberfarmsnc@gmail.com or by calling us at 704.516.9681. Thank you!
How long does processing take?
We typically are about 5-6 months from in-the-door to ready for pick up or shipping.
Why does processing take so long?
While most orders only take a few weeks to complete (depending on size or need for separation) each incoming order is sitting behind hundreds of pounds of previous orders. Additionally, we are currently operating with only hand-spinning, so if you order includes spinning you can plan to have it take an additional 1-3 months. There are simply too few mills to meet the need for processing.
How do I get my fiber to you?
We prefer to meet with our customers if at all possible, so we can go through your fiber with you and discuss your options - that way, you can also get a tour of the mill and see how your fiber will be processed if you’re interested. Just let us know when you plan to come, so we are not in the barn or out on errands when you arrive. You can also mail your fiber to us at Gober Farms 9231 Ferguson Rd, Charlotte, NC, 28227. Please email us to let us know it’s coming and we’ll keep an eye out and email you upon receipt.
Do you reject fiber?
Yes. We’ve tried to work with poor fiber before, and unfortunately it left both us and the customer dissatisfied. Infested fiber is immediately disposed of. Fleeces that are too matted. If you cannot pull apart the fiber with light to moderate effort -- neither can we. Matting is also an issue for those who dye in the grease.
We will reject fiber with too many burrs or wood shavings; burrs choke our separator and chip does not come out (it just gets smaller).
If your fiber needs separation for vegetation, but you will not authorize use of the separator, we will refuse to take an order that we cannot produce a good reputable product.
Can I get 100% Alpaca roving? Suri?
Huacaya, probably. Suri, no. Some alpaca is too slick and too short to hold together through the roving deck. Adding suri reduces the possibility of getting roving from the carder. We cannot run straight suri through our separator or carder. We recommend using suri like silk -- not about a 10% add-in to wool (sheep).
Can I get 100% pygora, angora, or Cashmere roving?
No. Pygora must be de-haired -- leaving the slick angora fiber. That slick fiber will not hold together through the roving deck off the carder, so customers get back separated cloud from pygora orders. Angora need not be separated if low in vegetation and guard hair. We recommend adding mohair/Cashmere -- not more than 50% -- to wool (sheep). Goat fiber will not make alpaca fiber run better.
We love to talk to fiber people!
If you have any questions about your order, our fiber, what we do, how we do it, or why -- please either email us at goberfarmsnc@gmail.com or call us at 704-516-9681.
Privacy & Safety
We do not store payment information, nor do we sell or voluntarily share your purchase or contact information with anyone.
Payment Methods
We use Square for invoice processing and accept all major debit and credit cards, cash, and can discuss other payment methods if needed.
Invoice Structure
Invoice is sent on completion of your order and is due to be paid in full 14 days from that date.
Customer Updates
We will take images of your fiber upon arrival (pre-wash) and weigh in immediately. We will update you with this information along with any recommendations for processing. Please note that Gober Farms retains the right to decline working with your fiber as discussed in the rejected fiber section if the fiber is not within working conditions. We will provide regular updates as your fiber moves throughout the milling process, and please do not ever hesitate to reach out if you have questions!
Customer Satisfaction
You can rest assured that our foremost desire is for you to have an end product with your fiber that is 100% satisfactory and profitable. As fellow fiber-farmers that love our animals and their product, we understand that they work hard for this and so have you. We’ve learned a tremendous amount over the last five years and are grateful to have been apprenticed by the oldest operational mill in Oregon when we purchased our Belfast Mini Mills equipment in 2024. Please know that we want this to be a conversation to ensure that we implement your feedback and attain the final product you desire. Upon your fiber drop off, we’ll review all of your product options, our work, and your craft or sales goals so we can help you on your fiber journey.